For early-stage product developers, the road from idea to tangible prototype can either be a launchpad—or a money pit.
Choosing the right rapid prototyping technique can save weeks of time, thousands in costs, and make or break your path to product-market fit.
Let’s cut through the noise. Here’s a tactical breakdown of the seven most effective rapid prototyping techniques, designed for startup-minded makers, bootstrapped innovators, and lean eCommerce entrepreneurs.
1. 3D Printing (Additive Manufacturing)
Best for: Early MVPs, form studies, quick design validation
Strengths: Speed, flexibility, low cost, minimal setup
Limitations: Lower durability, surface finish may require post-processing
3D printing for rapid prototyping has become the default starting point for physical product development. Whether you’re prototyping a pet gadget, a home automation device, or a novelty kitchen tool, 3D printing gives you the freedom to iterate without worrying about molds or tooling.
Key Advantages
- Design freedom: Create intricate geometries that are impossible to machine or mold.
Low-cost iteration: Change your CAD file, hit print, and you’re testing a new version by morning. - Multiple material options: PLA for affordability, ABS for impact resistance, TPU for flexibility.
When to Use It: You’re still figuring out dimensions, fit, and overall design. You want to test how it looks, feels, and functions—without investing in tooling.
PrototyperLab Insight: Many projects go straight from CAD to 3D printing using in-house FDM or resin printers. This can produce a viable functional prototype within 24–48 hours—accelerating early testing dramatically.
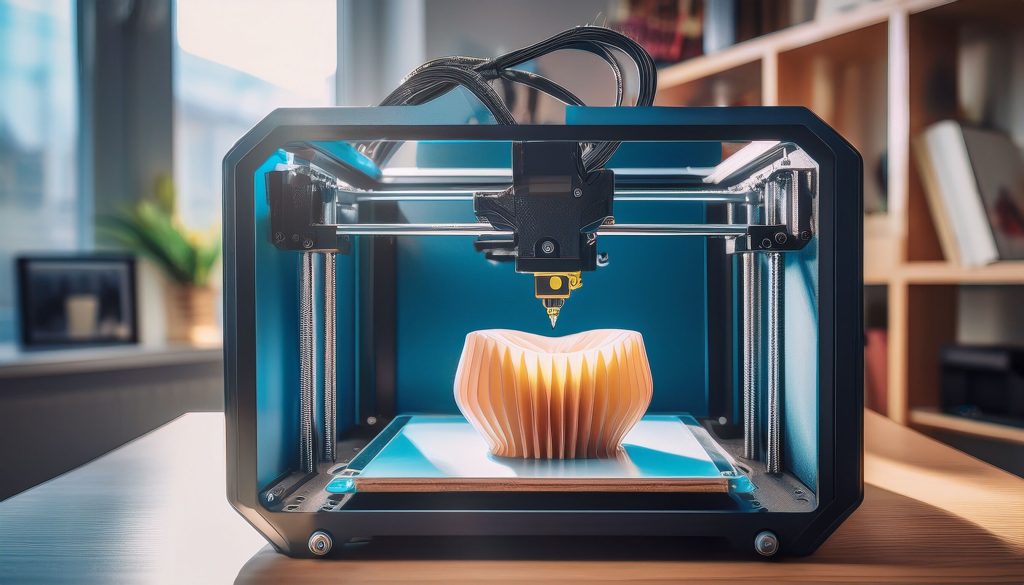
2. CNC Machining
Best for: Functional testing, high-precision mechanical parts, metal or hard plastic prototypes
Strengths: Tolerance accuracy, material realism, strength
Limitations: Higher cost and lead time than 3D printing
CNC machining for prototypes bridges the gap between rapid development and real-world performance. It’s indispensable when your product has moving parts, tight tolerances, or needs to survive stress testing.
Key Advantages
- Material realism: You can prototype in aluminum, stainless steel, POM, or even aerospace-grade plastics.
- Engineering validation: Ideal for testing strength, fit, and mechanical performance before mass production.
- Surface quality: Superior finishes and precision vs. printed parts.
When to Use It: Your 3D-printed prototype passed the visual test, but now it’s time for real-world durability. Especially relevant for load-bearing, structural, or performance-critical parts.
PrototyperLab Insight: For founders building functional prototypes of robotic parts or enclosures for electronics, CNC ensures each unit can be tested under final-use conditions.
3. Vacuum Casting
Best for: Low-volume production runs (20–100 units), user testing, presentation-quality prototypes
Strengths: End-use look and feel, consistent part replication
Limitations: Mold degradation over time, not ideal for sharp internal features
Vacuum casting allows you to replicate a master part—typically made with CNC or 3D printing—using silicone molds to produce multiple copies in production-grade materials.
Key Advantages
- Ideal for user testing: Parts can mimic injection-molded quality and finish.
- Flexible production: Produce short runs fast without committing to expensive molds.
- Material options: Wide variety of resins that simulate ABS, rubber, or polypropylene.
When to Use It: You’re preparing to soft-launch a product or send out pilot units to beta testers, influencers, or early backers. You need high-quality parts that look and feel like final production.
PrototyperLab Insight: Founders often use vacuum casting to manufacture 30–50 units for Amazon test listings or Kickstarter reward fulfillment before investing in injection tooling.
4. Silicone Molding (RTV – Room Temperature Vulcanization)
Best for: Soft-touch components, flexible parts, ergonomic testing
Strengths: Low tooling cost, great for textured or organic shapes
Limitations: Limited mold life (typically under 100 uses), some shrinkage
Silicone molding is ideal for replicating complex shapes in soft or rubber-like materials. It’s widely used for prototyping parts like gaskets, grips, or wearables.
Key Advantages
- Excellent for touch and ergonomics: Simulates soft plastic or rubber materials with realistic hand-feel.
- Short turnaround: A mold can be made in one day, and used to produce multiple units immediately.
- No heat or pressure required: Molding process is safe and low-impact, suitable for delicate features.
When to Use It: You’re prototyping parts that will be touched, squeezed, or worn. You need multiple units to compare shape or softness.
PrototyperLab Insight: Many clients use RTV molding to prototype fitness handles, baby products, or wearable accessories where texture and grip are critical.
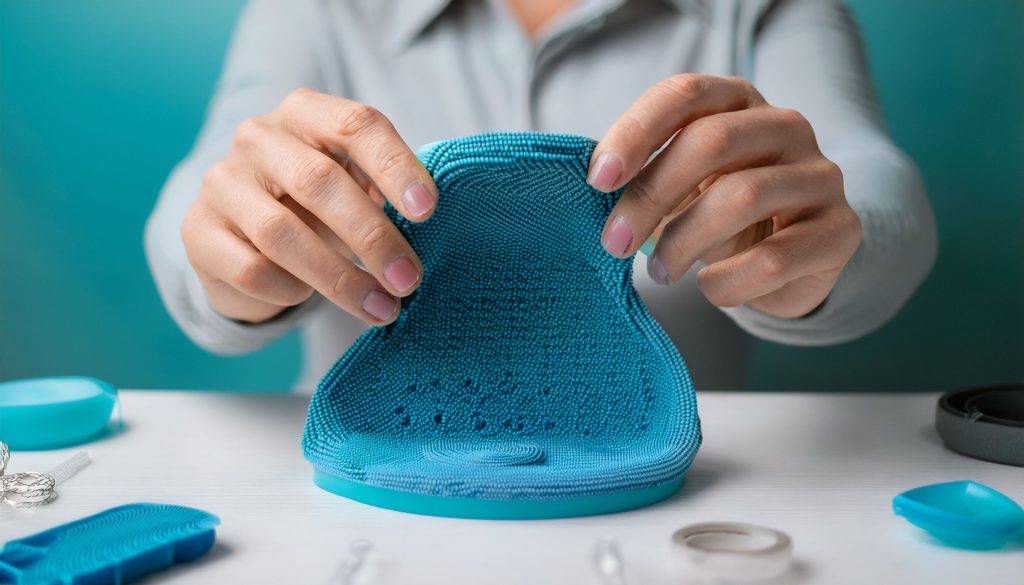
5. Laser Cutting
Best for: 2D shapes, faceplates, flat components, quick mockups
Strengths: Speed, affordability, precision for flat parts
Limitations: Limited to flat geometry, bonding required for 3D assembly
Laser cutting offers rapid production of flat geometries from sheet material, making it a go-to for housing parts, visual displays, or early UX mockups.
Key advantages:
- Ultra-fast: Same-day turnaround for design files under 30 minutes.
- Clean cuts: High dimensional accuracy and smooth edges.
- Material options: Acrylic, MDF, plywood, stainless steel sheets, and more.
When to Use It: You need flat parts or want to create quick assembly mockups. Ideal for packaging inserts, signage, or custom brackets.
PrototyperLab Insight: Projects combining laser-cut acrylic with 3D printed spacers or mounts often deliver impressive prototypes in both aesthetics and function within a day.
6. Sheet Metal Prototyping
Best for: Industrial or consumer-grade enclosures, durable mechanical components
Strengths: Structural integrity, scalability to production, thermal resistance
Limitations: Limited flexibility for complex geometries, requires forming and bending tools
Sheet metal prototyping is a cost-effective way to produce strong, production-ready parts quickly. It’s widely used in consumer electronics, IoT devices, and durable gear.
Key Advantages
- Durability: Perfect for parts that need to withstand drops, weather, or impact
- Production-friendly: Smooth transition from prototype to manufacturing
- Customization: Includes cutouts, embossing, and powder coating options
When to Use It: Your product needs to feel premium or survive rugged use. Think smart locks, camera mounts, or outdoor sensors.
PrototyperLab Insight: Founders looking to create weatherproof enclosures often prototype in aluminum sheet metal to ensure their product holds up in harsh conditions before investing in die casting.
7. Injection Molding (Rapid Tooling)
Best for: Beta launch, investor demos, retail-ready packaging
Strengths: High-quality finish, production-level detail, low per-unit cost at scale
Limitations: Higher upfront cost, slower than other rapid methods
While injection molding is traditionally slow and expensive, rapid tooling brings the advantages of this technique into the hands of early-stage entrepreneurs.
Key Advantages
- Final production quality: What you mold is what you ship.
- Low-cost units after tooling: Great ROI once tooling cost is covered.
- Certifiable parts: Meet regulatory or packaging standards.
When to Use It: You’ve validated the prototype and are ready to produce 100–1,000 units for beta launch, sales, or pre-order fulfillment.
PrototyperLab Insight: For clients who’ve already prototyped with 3D printing and vacuum casting, we can transition to small-batch injection molding to meet retail or DTC launch standards—while keeping total costs well under the $10K threshold.
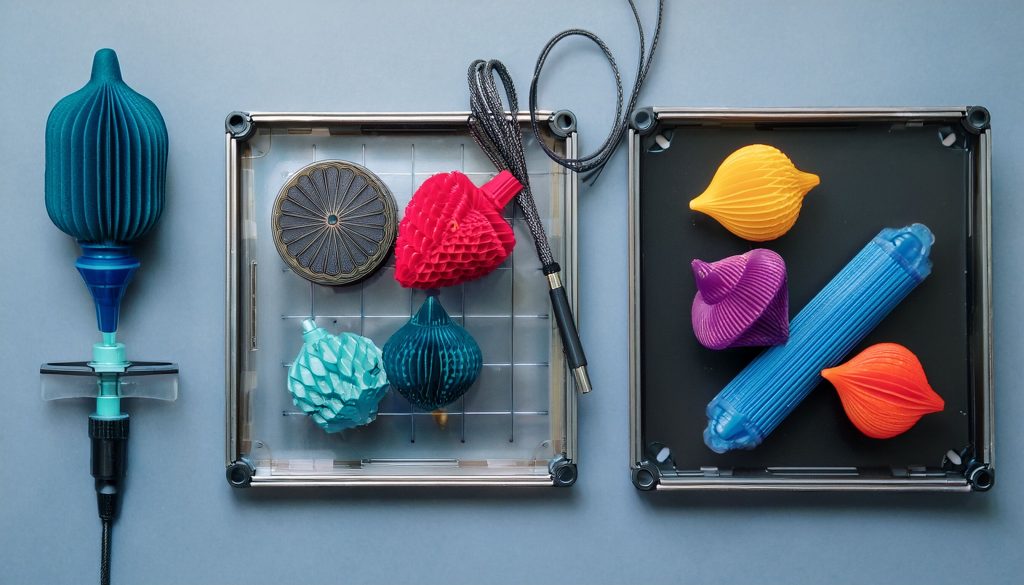
Final Comparison: What’s Best for Your Stage?
Development Stage | Recommended Technique(s) |
Concept Validation | 3D Printing, Laser Cutting |
Functional Testing | CNC Machining, Silicone Molding |
Ergonomic & User Testing | RTV Molding, Vacuum Casting |
Pilot Production (20–100 units) | Vacuum Casting, Sheet Metal Prototyping |
Pre-Launch Manufacturing | Injection Molding (Rapid Tooling) |
Build Fast. Launch Smart. Iterate Without Regret.
The biggest mistake early-stage founders make? Waiting too long—or spending too much—before testing.
Rapid prototyping techniques are tools, not trophies. The goal isn’t to build a perfect prototype. It’s to build the right prototype, fast enough to learn and iterate.
PrototyperLab makes that happen with:
- 7-Day Prototyping
- Small Batch Production (20+ units)
- $25/hour Transparent Engineering
- U.S. Legal Contracts + Vietnam Manufacturing
Whether you’re building a modular pet gadget, a smart fitness tool, or a quirky novelty toy, the fastest way to market is through prototyping you can afford—and trust.
Need help choosing the right method for your product idea?